When we bought this house 5 years ago, we did it with the intention of finishing the basement. The basement is below grade on one side, above grade on two, and next to the crawlspace on the fourth side, and it has good ceiling height already.
We’ve already waterproofed it with a perimeter drain, vapor barriers, and a sump pump (as well as a sump pump in the crawlspace with some interior drainage there, too), and our 2023 landscape project did a lot with moving water away from the house on the outside.
The Plan
The plan is to have a quarter of the basement as a finished laundry (the laundry machines are already down there), a quarter of it unfinished for utility and storage, and the remaining as finished space that will have my desk, some seating and a tv, and a space for home exercise. Really, the seating and tv are the only functions that will be new to the space. I was already working in the unfinished basement, and Megan was already doing workouts down there.
We’re working with Nat at Good Wood Works on this. One of my favorite ideas he brought right out of the gate was removing four of the six weight-bearing posts, which will really help to open up the landing of the stairs into the finished space.
Pre-Work Work
Early in the project, Nat spent a day in the basement while his subcontractors came in, looked at things, and took measurements to provide estimates. Two unexpected additions to the project came from this: encapsulating and dehumidifying the crawlspace and electrical upgrades.
As mentioned, the crawlspace already had a sump pump and some interior drainage. Apparently that wasn’t enough, so encapsulating and dehumidifying that space got added to improve the air of the basement and the house.
For the electrical, we needed a bigger panel and AFCI/GFCI breakers, and we needed hardwired smoke detectors throughout the house to meet current code. Our county requires a detector on every floor and in each bedroom.
An engineer also came by to see what kind of header would be needed to handle the load for the poles coming out.
Thanksgiving Week
Work began the week of Thanksgiving. Monday the crawlspace was encapsulated, and Tuesday the crawlspace dehumidifier was installed.
Week After Thanksgiving
Tuesday and Wednesday
Tuesday the electrician replaced the panel. Wednesday he installed the smoke detectors throughout the house ran some cable in the basement.
Thursday and Friday
Thursday and Friday was mostly framing. Three of the poles were cut out on Thursday, and the fourth on Friday when they put in the header.
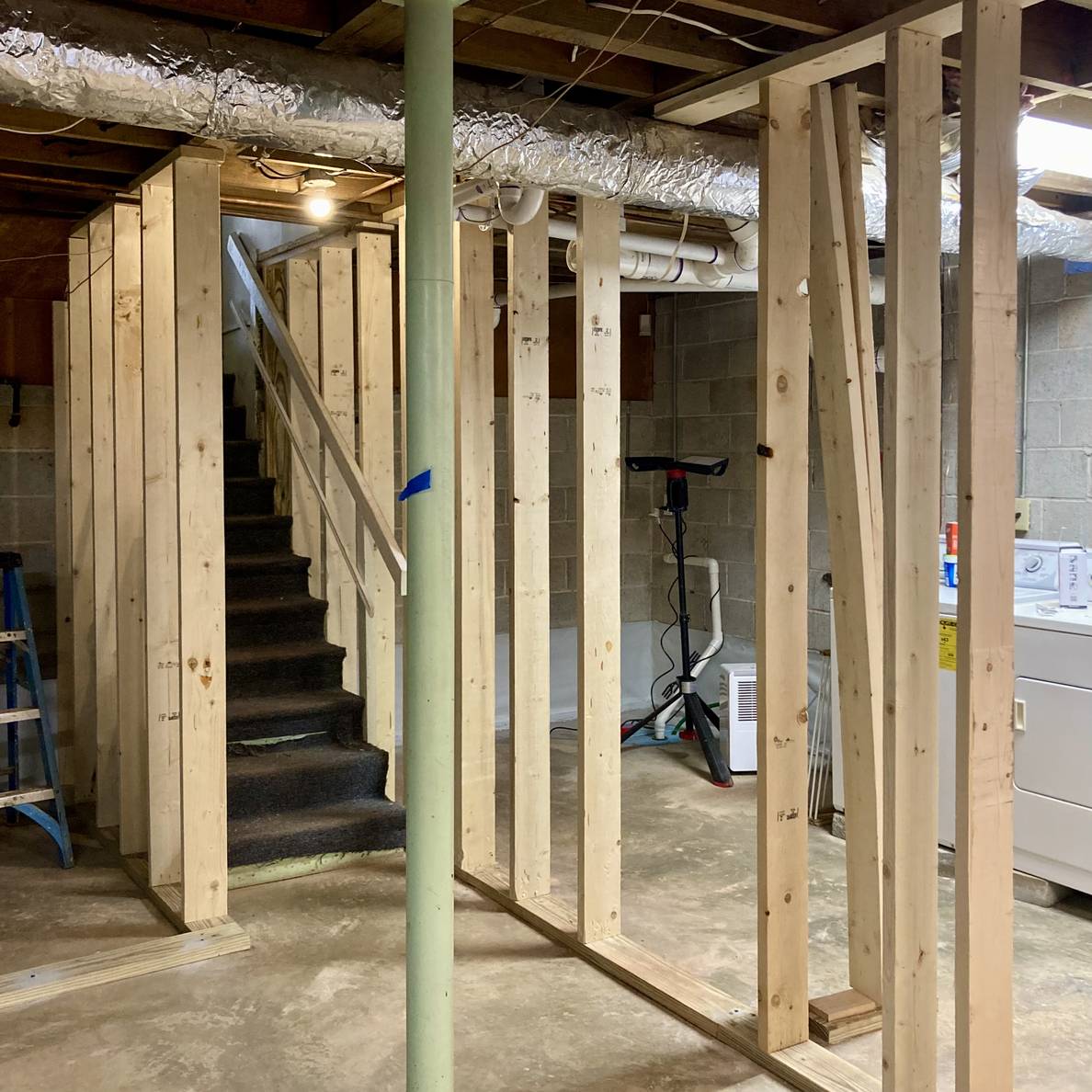
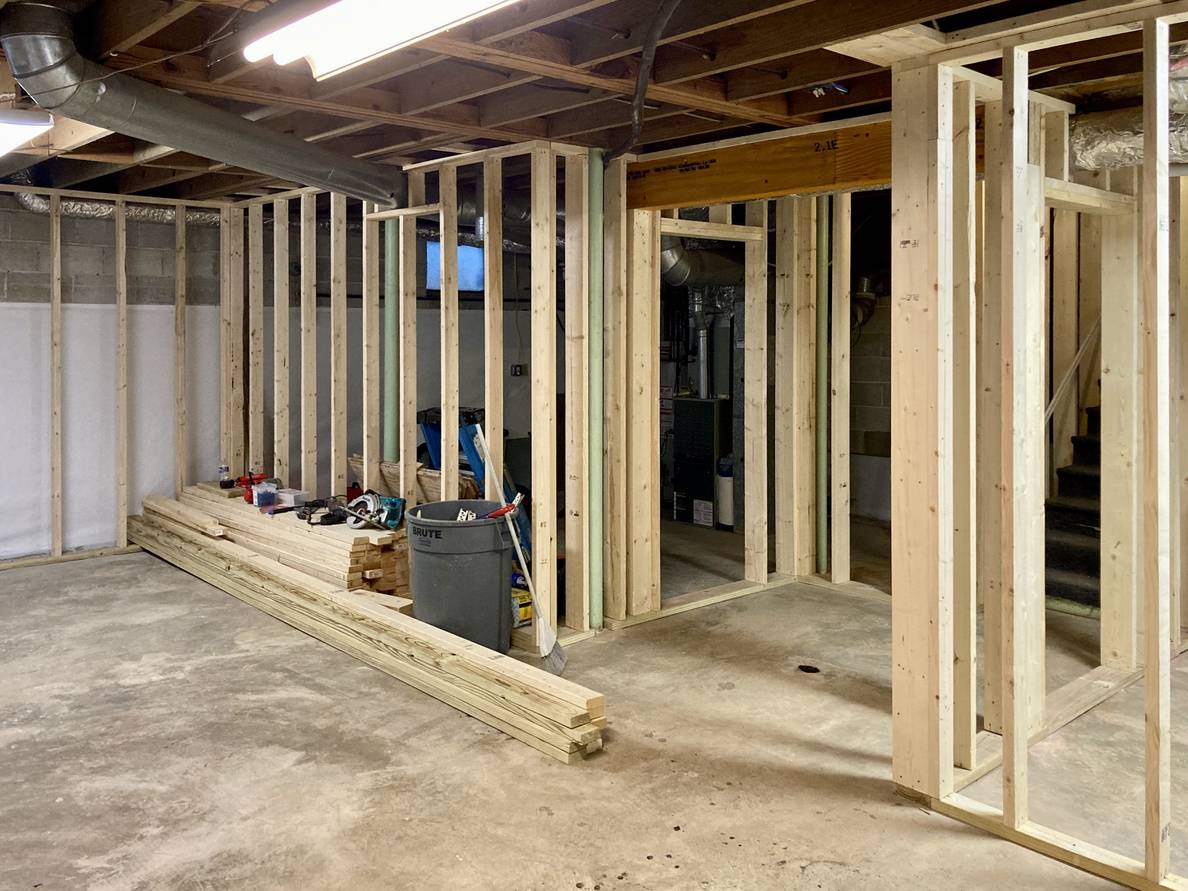
This Week
Monday, Nat and his crew continued framing. Yesterday, they were able to add an additional support that allowed them to remove a section of a floor joist to get us a bit more head clearance over the stairs.

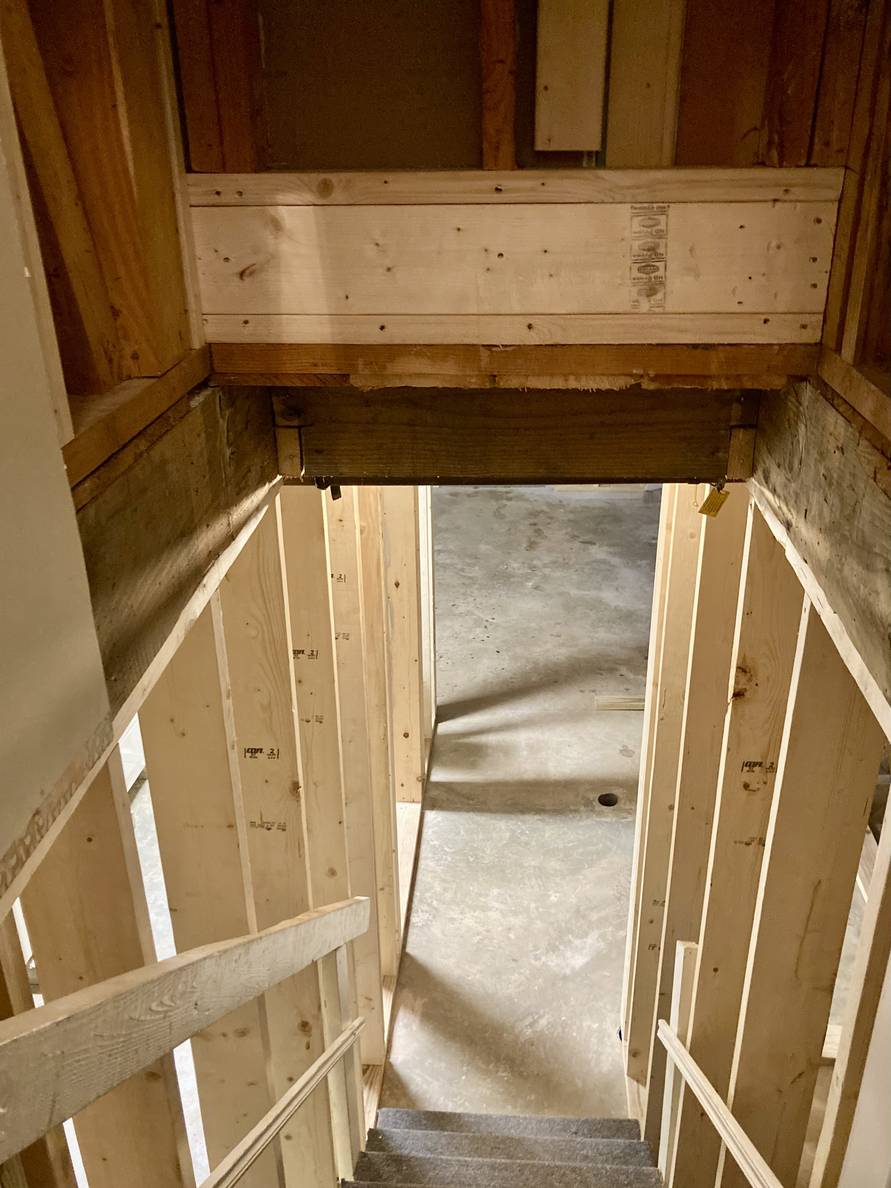
Moving Forward
Lots still to be done. I hope to post more granular updates moving forward.